La capacidad de producción es una piedra angular en la gestión operativa de cualquier empresa, en particular en el sector industrial. Comprender a fondo este concepto es esencial para asegurar un manejo efectivo y eficiente de los recursos productivos.
La capacidad de producción no solo se refiere a cuánto puede producir una unidad productiva en un período determinado, sino que también abarca la eficiencia y calidad de estos procesos.
Una comprensión clara de la capacidad de producción es vital, ya que influye directamente en la capacidad de una empresa para cumplir con los plazos de entrega, responder a las demandas del mercado y mantener la satisfacción del cliente. Y de eso nos encargaremos en este artículo.
¿Qué es capacidad de producción?
La capacidad de producción se refiere al máximo rendimiento que puede alcanzar una unidad productiva, como una planta o equipo, en un período determinado.
Este concepto no solo abarca la cantidad de bienes que se pueden fabricar, sino también la eficiencia y calidad con la que se realizan estos procesos. Entender la capacidad de producción es crucial para el manejo efectivo de cualquier empresa, especialmente en el sector industrial.
¿Por qué es tan importante conocer la capacidad de producción?
Comprender la capacidad de producción es valioso en cualquier empresa, especialmente en sectores donde la eficiencia y puntualidad son esenciales. Pero, ¿por qué es tan importante?
Permite definir los tiempos de entrega
Al tener una idea precisa de la capacidad de producción, una empresa puede ofrecer estimaciones de entrega realistas. Esto es más que una simple cifra; se trata de satisfacer las expectativas del cliente y evitar promesas que no se pueden cumplir.
La decepción del cliente debido a estimaciones erróneas puede afectar la reputación y la fidelidad a largo plazo.
Facilita una planificación de la producción más efectiva
Esta planificación informada permite una toma de decisiones ágil y reduce la incertidumbre en la satisfacción de la demanda. Aquí, la clave es la anticipación: poder prever y ajustar la producción en función de las necesidades del mercado.
Puedes conocer tu tasa de utilización
Comparando la capacidad de producción con lo que realmente se produce, puedes evaluar qué tan bien se están utilizando tus recursos. Esta comparación es esencial para identificar áreas de mejora y alcanzar un equilibrio óptimo entre operación y costos.
Es un indicador de rendimiento
No solo para la empresa en términos de eficiencia y productividad, sino también como una herramienta motivacional para los equipos, incentivándolos a cumplir y superar los objetivos de producción establecidos.
Te ayudamos a elegir un ERP a tu medida (GRATIS)
Somos expertos asesorando empresas en la elección de su ERP, llena el formulario y recibe una asesoría gratuita
Te responderemos a la mayor brevedad posible.
Tipos de capacidad de producción
Entender los tipos de capacidades de producción es esencial para gestionar eficientemente los recursos de una empresa. La capacidad de producción no es un concepto unitario; varía según diversos factores y circunstancias.
Veamos cuáles son:
1. Capacidad instalada de producción
Es la capacidad máxima de producción que puede alcanzar una instalación bajo condiciones ideales. Se calcula con base en las especificaciones técnicas de los equipos y la planificación de la producción inicial. Esta capacidad no considera paradas por mantenimiento, cambios en la producción o problemas operativos.
2. Capacidad práctica o efectiva
Menos idealizada que la capacidad teórica, la capacidad efectiva toma en cuenta las ineficiencias y los problemas reales de la producción, como el mantenimiento de equipos, los descansos del personal y las interrupciones menores. Se acerca más a lo que una empresa puede esperar en condiciones normales de operación.
3. Capacidad utilizada de producción
Es la parte de la capacidad efectiva que realmente se está utilizando para producir. Este concepto es crucial para entender la utilización de la capacidad.
Por ejemplo, una fábrica podría tener una capacidad efectiva para producir 1000 unidades al día, pero si solo produce 800, su capacidad utilizada de producción es del 80%.
4. Capacidad ociosa
Refiere a la parte de la capacidad que no se está utilizando. Siguiendo el ejemplo anterior, si la capacidad efectiva es de 1000 unidades pero solo se producen 800, hay una capacidad ociosa del 20%. Este tipo de capacidad puede indicar una oportunidad para aumentar la capacidad productiva sin incurrir en costos adicionales significativos.
5. Capacidad de cuello de botella
En cada proceso de producción, suele haber una etapa que limita la velocidad total del proceso. Esta es la capacidad de cuello de botella, y determina la capacidad máxima de toda la línea de producción.
6. Capacidad flexible
Se refiere a la capacidad de un sistema productivo para adaptarse a diferentes tipos de productos o a cambios en el volumen de producción. Esta flexibilidad es vital en entornos de producción que enfrentan variaciones frecuentes en la demanda.
¿Cómo se calcula la capacidad de producción? Fórmulas
Calcular la capacidad de producción es una tarea esencial para cualquier empresa de manufactura, ya que proporciona una base para la eficiente planificación de la producción y la administración de la capacidad. Vamos a desglosar este proceso en pasos detallados para que puedas entender cómo se realiza este cálculo y aplicarlo en tu propio contexto.
1. Calcular la producción real
Primero, mide la producción real en un período pasado. Esto implica contar el número de productos terminados en un tiempo específico, como una hora, un día o una semana. Para obtener una capacidad promedio de producción, suma los resultados de diferentes períodos y divídelos por el número de períodos.
Aunque esta medida proporciona una buena base, no refleja la capacidad total ya que no considera posibles variaciones en el trabajo, horas laborables, calificación de los trabajadores o fluctuaciones en la oferta.
2. Calcular manualmente la capacidad de producción
Este cálculo es más complejo y requiere dos parámetros principales: la capacidad de la máquina por hora y el tiempo de producción.
- Capacidad de la Máquina por Hora: Calcula la cantidad total de tiempo disponible para trabajar en las máquinas necesarias para crear un producto. Esto se logra multiplicando el número de máquinas utilizables por el número de horas de trabajo.
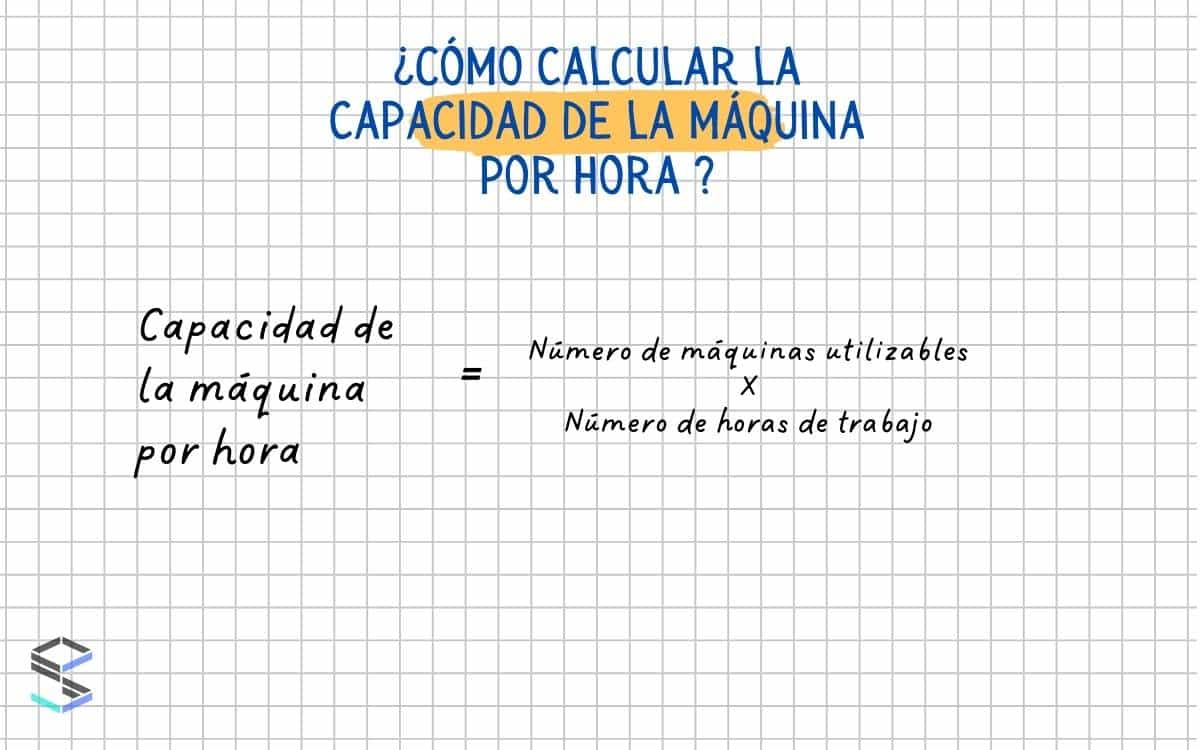
- Tiempo de Producción: Es el tiempo total que un producto pasa siendo procesado en la línea de producción. Si mides la capacidad por proceso individual, se conoce como tiempo de ciclo.
3. Capacidad de producción de un solo producto
Para calcular la capacidad de producción de un solo producto se debe dividir la capacidad de la máquina por hora según el tiempo de producción.
Por ejemplo, si tienes 5 máquinas y los empleados trabajan en turnos de 8 horas, con 6 segundos para procesar un producto, la capacidad de producción será 24000 unidades por turno de 8 horas.
4. Capacidad de producción de varios artículos
Cuando una planta produce varios productos, el cálculo se complica un poco más. Multiplica el tamaño del pedido de cada producto por su tiempo de producción, suma los resultados de todos los productos y divídelos por la capacidad de la máquina por hora de la planta.
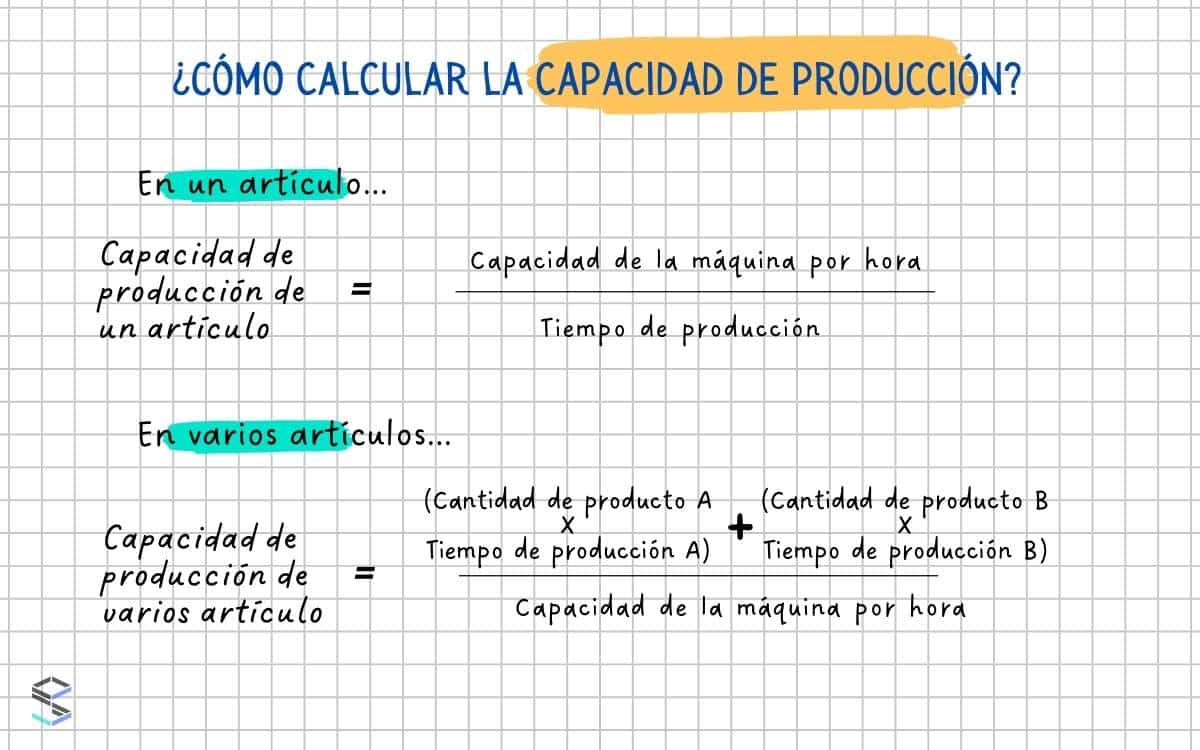
5. Determinar el índice de utilización de la capacidad
Finalmente, para calcular el indicador de capacidad de producción referente a la utilización puedes usar la siguiente fórmula:
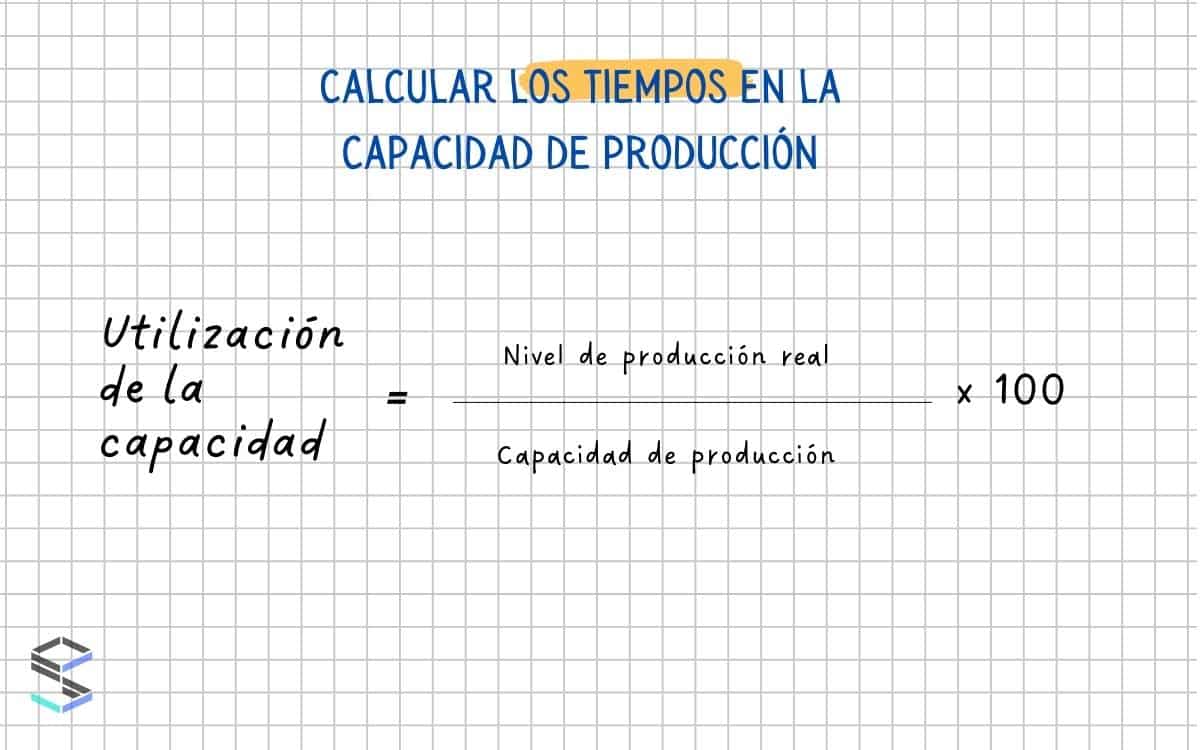
Este índice es crucial para evaluar la eficacia operativa y los costos. Una tasa de utilización óptima ronda el 85%, ya que una tasa más alta podría llevar a una depreciación acelerada de las estaciones de trabajo o dificultades para responder a aumentos repentinos en la demanda.
La administración de la capacidad de producción es un proceso crucial para asegurar que una empresa pueda satisfacer eficientemente la demanda del mercado, manteniendo al mismo tiempo una operación rentable y sostenible. La planificación y gestión de esta capacidad implican equilibrar de manera efectiva los recursos disponibles con las necesidades de producción, teniendo en cuenta tanto la demanda actual como las proyecciones futuras. Veamos cómo se puede administrar efectivamente esta capacidad:
1. Entiende la división de trabajo y recursos
El primer paso es comprender en detalle cómo se distribuye el tiempo de trabajo y los recursos necesarios para cada tarea. Esto implica que cada empleado debe tener claramente definidas sus funciones, horarios y los recursos que requiere para desempeñar su trabajo eficientemente. La utilización de herramientas como hojas de cálculo de Excel para clasificar estos datos puede ser muy útil.
2. Estima los recursos necesarios
La siguiente etapa es calcular la cantidad total de mano de obra, inventario y capital necesarios para cumplir con los objetivos de producción. Este cálculo debe considerar todos los factores de producción, incluyendo la capacidad empresarial, para garantizar una estimación precisa y realista.
3. Prioriza las cargas de trabajo
Una de las tareas más críticas en la administración de la capacidad de producción es la priorización de las cargas de trabajo. Esto implica determinar qué tareas son más urgentes o críticas y asegurar que los recursos necesarios estén disponibles para completarlas a tiempo.
4. Planea rutas estratégicas
Para empresas y proyectos de mayor envergadura, definir una estrategia de planificación de la capacidad productiva es esencial. Esta estrategia debe anticiparse a posibles interrupciones, reduciendo riesgos y manteniendo un flujo de trabajo constante para satisfacer la demanda.
5. Supervisa las cargas de trabajo
Finalmente, una vez implementada la estrategia, es vital continuar supervisando la carga de trabajo. Esto permite detectar y solucionar rápidamente cualquier problema que impida satisfacer eficientemente las necesidades de producción.
Los principales problemas en la capacidad de producción
varios problemas pueden afectar la capacidad de producción de una empresa. Estos problemas, si no se gestionan adecuadamente, pueden llevar a una disminución en la eficiencia, aumentar los costos y reducir la satisfacción del cliente. Es crucial identificar y abordar estos problemas para mantener una operación fluida y rentable.
1. Sub utilización de la capacidad
Uno de los problemas más comunes es la sub utilización de la capacidad instalada. Esto ocurre cuando la unidad productiva no opera a su máxima eficiencia, lo que resulta en una baja tasa de utilización.
La sub utilización puede deberse a una demanda de mercado insuficiente, ineficiencias en los procesos de producción o limitaciones en la gestión de la cadena de suministro. (Un tip: el modelo SCOR puede ayudarte a solucionar este problema)
2. Sobrecapacidad
Contrario a la sub utilización, la sobrecapacidad ocurre cuando la capacidad de producción de una empresa supera la demanda del mercado. Esto puede llevar a un exceso de inventario, aumentar los costos de almacenamiento y reducir la liquidez.
3. Cuellos de botella en la producción
Los cuellos de botella se producen cuando un paso específico en el proceso de producción limita la velocidad general del proceso. Esto puede deberse a una maquinaria inadecuada, fallas en los equipos o una mala planificación de la capacidad.
Identificar y solucionar estos cuellos de botella es vital para mejorar la eficiencia general.
4. Variabilidad en la calidad de la producción
La inconsistencia en la calidad del producto final puede ser un indicativo de problemas en la capacidad de producción. Puede deberse a una capacitación insuficiente del personal, equipos obsoletos o un control de calidad deficiente.
5. Falta de flexibilidad
En el actual entorno de mercado, donde la demanda puede fluctuar rápidamente, una falta de flexibilidad en la capacidad de producción puede ser problemática. La incapacidad para adaptarse a cambios en la demanda o para modificar la producción según las necesidades del mercado puede llevar a pérdidas significativas.
¿Cómo aumentar la capacidad de producción?
¿Y si ya me hice cargo de la administración de la capacidad de producción pero no veo los resultados esperados? En ese caso es hora de optimizar.
Aumentar o mejorar la capacidad de producción consiste en optimizar los recursos existentes para incrementar la producción sin incurrir necesariamente en grandes costos de producción.
Veamos algunas estrategias y métodos eficaces para lograr este objetivo.
1. Optimiza la metodología de fabricación
Implementar prácticas de fabricación ajustada es un enfoque efectivo. Esto implica eliminar los desechos y mejorar la eficiencia en cada etapa de tu plan maestro de producción.
Técnicas como la teoría de las restricciones (TOC) ayudan a identificar y gestionar los cuellos de botella, mientras que métodos como SMED (Single Minute Exchange of Dies) reducen los tiempos de cambio, incrementando así la capacidad productiva.
2. Mejora los procesos empresariales
Una mejor planificación de la producción y la gestión de procesos puede aumentar significativamente la capacidad. Utilizar enfoques como el justo a tiempo (JIT) optimiza la producción y reduce los costos generales.
La subcontratación de ciertos subconjuntos y el aumento del control de la cadena de suministro son también tácticas viables para mejorar la eficiencia.
3. Utiliza un ERP de fabricación
La implementación de un sistema ERP de fabricación puede ser un cambio transformador.
Aunque requiere una inversión inicial, estas soluciones basadas en la nube son cada vez más accesibles y ofrecen una funcionalidad robusta para optimizar la capacidad de producción a largo plazo.
4. Aumenta los turnos y las horas extras
Para responder a un aumento repentino de la demanda, agregar o extender turnos o incrementar las horas extras puede ser una solución a corto plazo, especialmente cuando la maquinaria aún no se utiliza a pleno rendimiento.
5. Subcontratación de la producción
Cuando la maquinaria ya opera a su máxima capacidad y no es posible un aumento interno, subcontratar parte de la producción puede ser una manera eficiente de satisfacer un aumento repentino de la demanda.
6. Entiende las limitaciones de la capacidad de producción
Identificar si las limitaciones son por oferta (capacidad de producción propia del proceso) o por demanda del mercado es crucial.
En caso de restricciones por oferta, el enfoque debe estar en mejorar los cuellos de botella. Si la limitación es por demanda, estrategias como marketing agresivo, promociones o diversificación de productos pueden ser efectivas.
7. Evalúa qué sistema utilizar: «Pull» versus «Push»
Entender la demanda es fundamental para determinar la capacidad necesaria. A diferencia de los sistemas «push», donde la producción se anticipa a la demanda, los sistemas «pull» se activan solo cuando hay una demanda real del cliente.
Esto ayuda a alinear la planificación de la capacidad con el factor limitante, ya sea la demanda o la capacidad del cuello de botella.
Conclusión
Administrar eficientemente la capacidad de producción es un elemento crucial para el éxito de cualquier empresa en el sector de la manufactura. Desde la comprensión de los diferentes tipos de capacidad hasta la implementación de estrategias para su optimización y mejora, cada aspecto juega un papel vital en el mantenimiento de una operación productiva efectiva.
Los desafíos, como la subutilización o la sobrecapacidad, los cuellos de botella y la variabilidad en la calidad de producción, requieren una atención cuidadosa y estrategias bien pensadas. Ya sea a través de la optimización de los procesos de fabricación, la mejora de la planificación empresarial, o la adopción de tecnologías avanzadas, es esencial para una empresa mantenerse ágil y adaptarse a las cambiantes demandas del mercado.